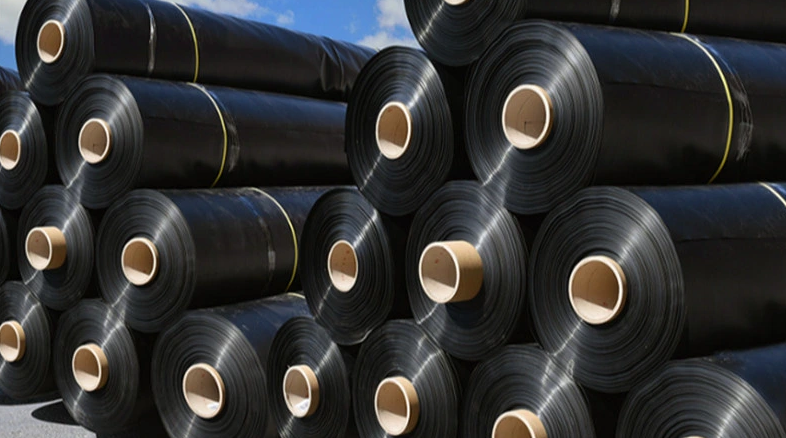
As the demand for high-quality materials in construction, agriculture, and various industries continues to rise, the role of HDPE sheets manufacturers becomes increasingly pivotal. This blog takes you behind the scenes, exploring the intricate process of manufacturing High-Density Polyethylene (HDPE) sheets and the commitment to excellence that distinguishes a reputable manufacturer.
The Art of HDPE Extrusion
1. Raw Material Selection
The journey begins with the careful selection of raw materials. Reputable HDPE sheets manufacturers prioritize the use of virgin resin, ensuring optimal material purity and consistency. This commitment to quality raw materials lays the foundation for the superior properties that HDPE sheets are known for, including durability, flexibility, and resistance to environmental factors.
2. Extrusion Process Precision
HDPE extrusion is a meticulous process where the chosen resin undergoes heating and shaping to form continuous sheets. Manufacturers invest in state-of-the-art extrusion machinery, leveraging advanced technology to achieve precise thickness, uniformity, and surface quality. The extrusion process is a delicate balance of temperature, pressure, and speed, demanding expertise to produce sheets that meet stringent quality standards.
Quality Control Measures
1. Thickness and Dimension Checks
Ensuring the uniform thickness of HDPE sheets is paramount. Manufacturers implement rigorous quality control measures, utilizing specialized equipment to measure and verify the thickness of each sheet. Dimensional accuracy is equally scrutinized to meet the specified requirements for various applications, from construction to agricultural use.
2. Material Testing for Strength and Durability
Quality manufacturers conduct thorough material testing to verify the strength and durability of HDPE sheets. Tensile strength, impact resistance, and other mechanical properties are assessed to guarantee that the sheets meet or exceed industry standards. This commitment to quality ensures that the end-users receive materials that withstand the rigors of their intended applications.
Customization Capabilities
1. Tailoring Sheets for Diverse Applications
Reputable HDPE sheets manufacturers understand the diverse needs of their clientele. Whether the sheets are destined for construction projects, agricultural applications, or specialized industrial uses, customization is key. The ability to tailor HDPE sheets to specific thicknesses, sizes, and even colors showcases the manufacturer’s commitment to meeting the unique demands of each customer.
2. Additives for Enhanced Properties
Incorporating additives into the manufacturing process allows for the enhancement of specific properties in HDPE sheets. UV stabilizers, antimicrobial agents, or flame retardants can be introduced to meet the requirements of different applications. A manufacturer’s capability to adapt and innovate with additives demonstrates a commitment to providing solutions that go beyond standard offerings.
Sustainable Practices
1. Recyclability Initiatives
In an era focused on sustainability, leading HDPE sheets manufacturers embrace environmentally conscious practices. This includes the incorporation of recycled content into their products, contributing to the circular economy. Manufacturers committed to recyclability are not just producers of materials; they are stewards of responsible and sustainable manufacturing practices.
2. Energy-Efficient Production Facilities
Sustainability goes hand in hand with energy efficiency. Recognizing this, forward-thinking manufacturers invest in modern and energy-efficient production facilities. Utilizing technology that minimizes energy consumption not only reduces environmental impact but also positions the manufacturer as a responsible contributor to a greener future.
Technological Innovations
1. Smart Manufacturing Systems
The evolution of HDPE sheets manufacturing isn’t stagnant; it’s a dynamic journey marked by technological advancements. Forward-thinking manufacturers embrace smart manufacturing systems, integrating automation and data analytics to optimize production processes. This not only enhances efficiency but also allows for real-time monitoring, ensuring consistent quality across every batch.
2. Precision Control through Robotics
In the pursuit of perfection, some manufacturers deploy robotic systems for intricate tasks within the production line. Robotic precision ensures that cutting, shaping, and finishing processes adhere to exact specifications. This level of automation not only elevates the precision of HDPE sheets but also contributes to the overall efficiency of the manufacturing ecosystem.
Research and Development Initiatives
1. Innovative Material Formulations
Leading HDPE sheets manufacturers invest in research and development to push the boundaries of material performance. This includes exploring innovative formulations that enhance specific properties. Whether it’s developing sheets with increased UV resistance or incorporating nanotechnology for improved strength, ongoing R&D initiatives drive the evolution of HDPE sheets.
2. Adapting to Industry Trends
Staying at the forefront of industry trends is crucial. Manufacturers actively engage in market research to identify emerging needs and trends, allowing them to adapt their product offerings accordingly. This responsiveness ensures that the HDPE sheets produced align with the latest industry demands, making them indispensable in a rapidly evolving market.
Global Sustainability Commitments
1. Carbon-Neutral Manufacturing Practices
In an era of heightened environmental awareness, reputable HDPE sheets manufacturers take proactive steps towards carbon neutrality. From adopting renewable energy sources to implementing waste reduction programs, these initiatives contribute to a more sustainable and eco-friendly manufacturing footprint. Choosing HDPE sheets from manufacturers with strong sustainability commitments aligns with global environmental goals.
2. Circular Economy Participation
Manufacturers are increasingly embracing the principles of a circular economy. This involves not only incorporating recycled content into their products but also actively participating in take-back programs. By facilitating the recycling of end-of-life HDPE sheets, manufacturers contribute to the circularity of materials, minimizing waste and reducing the environmental impact.
Global Outreach and Collaborations
1. Cross-Industry Collaborations
The influence of HDPE sheets extends beyond individual industries. Manufacturers engage in cross-industry collaborations to explore novel applications and unlock new potentials. Whether partnering with architects, engineers, or researchers, these collaborations foster innovation and broaden the horizons of HDPE sheet applications.
2. International Standards Adherence
Reputable manufacturers adhere to international standards, ensuring that their products meet or exceed regulatory requirements. This commitment not only speaks to the quality of the manufactured HDPE sheets but also facilitates global market access. Buyers worldwide can trust in the consistency and reliability of sheets produced by manufacturers dedicated to upholding international standards.
Future Horizons: Embracing Change
As we gaze into the future of HDPE sheets manufacturing, the narrative is one of continuous evolution and adaptation. Technological advancements, sustainable practices, and global collaborations are propelling the industry forward. Choosing HDPE sheets from manufacturers at the forefront of these advancements ensures not just access to materials but a partnership in shaping the industries of tomorrow.